Originally posted by rickgeo
View Post
Last night Carl and I got the cam tolerances set. They had to be free to a maximum of .005 of play.
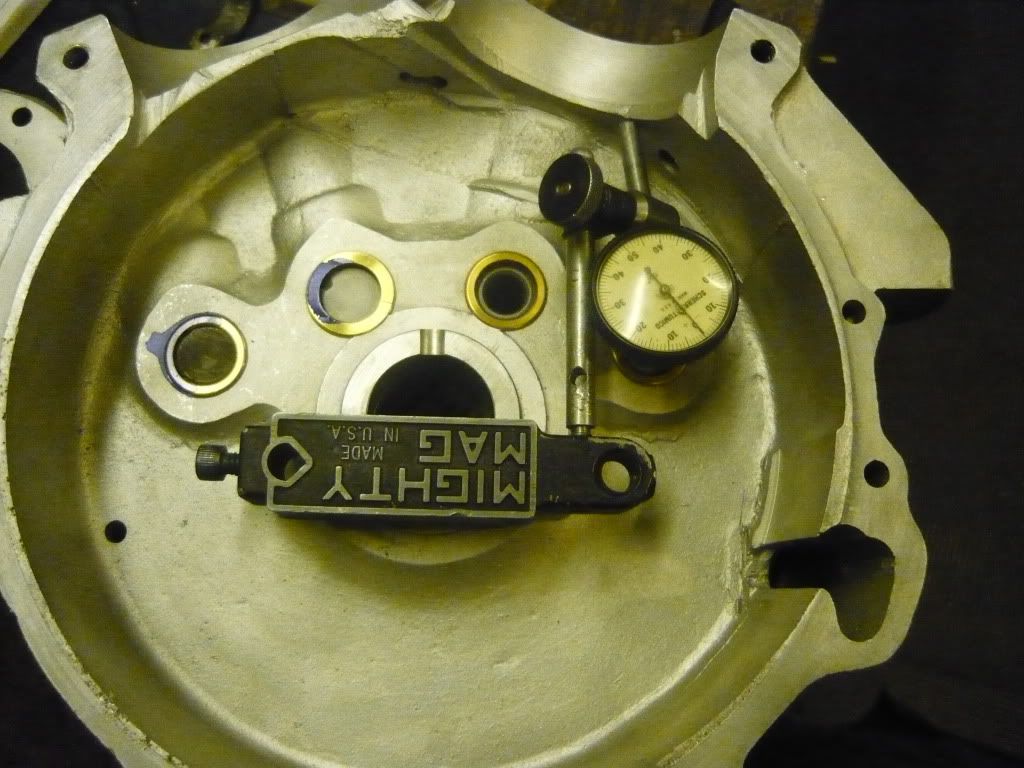
After we got them all set up, I stayed up and cleaned the cases really good and taped them to get painted.
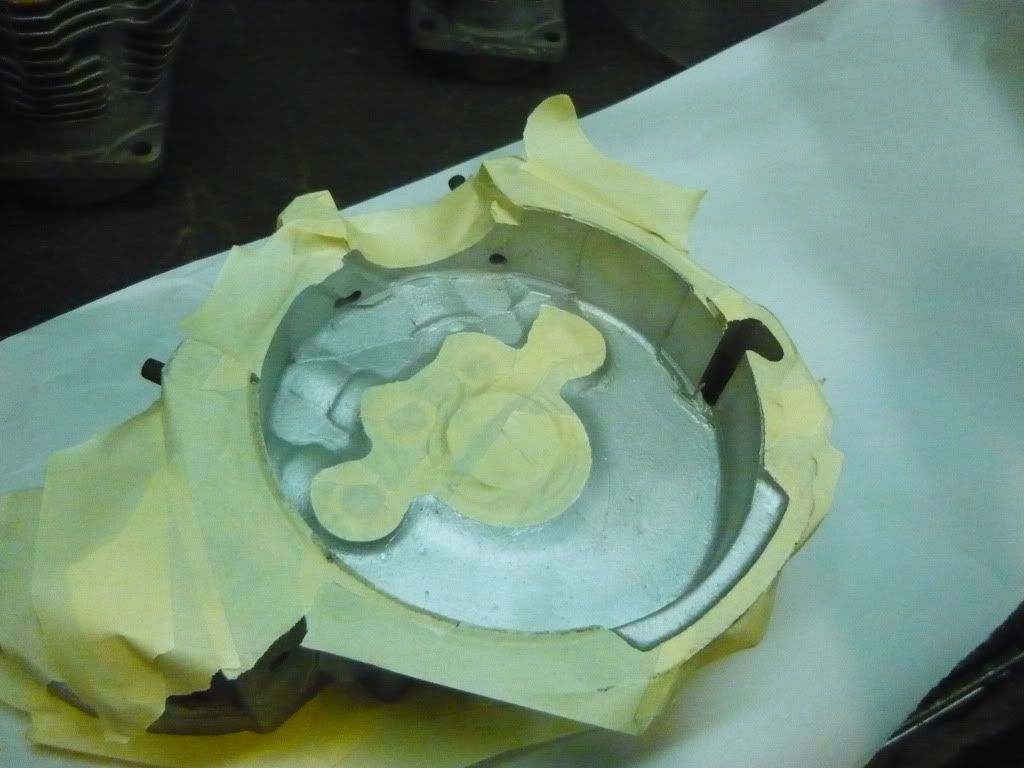
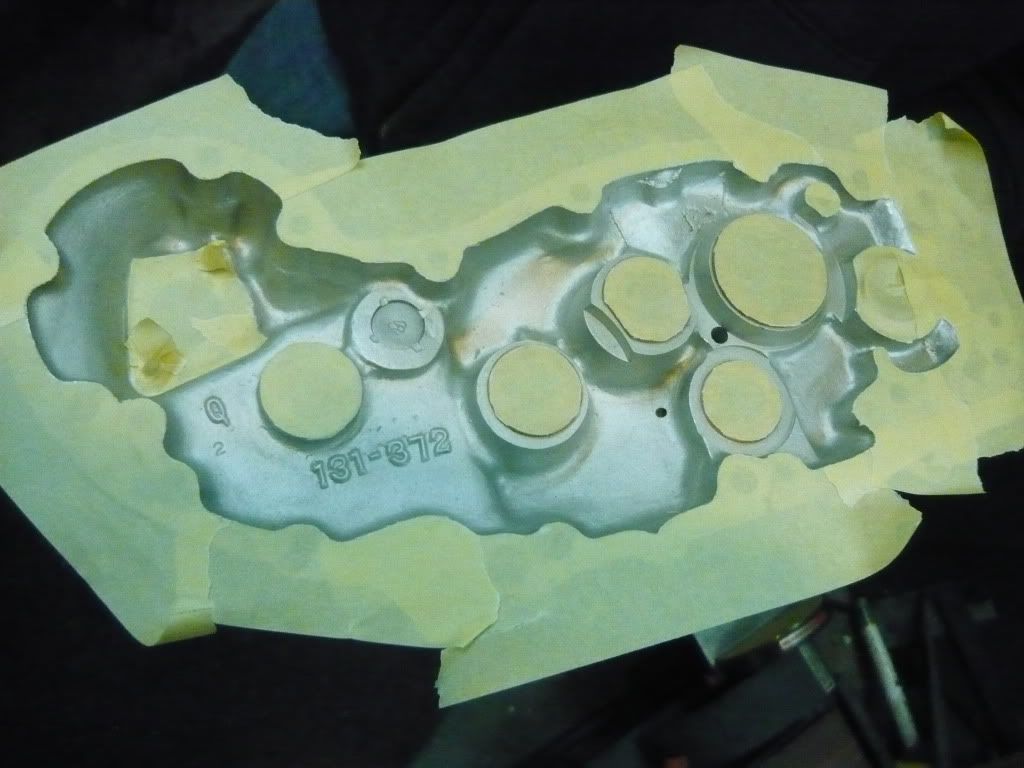
I just finished painting them to seal the inside this morning.
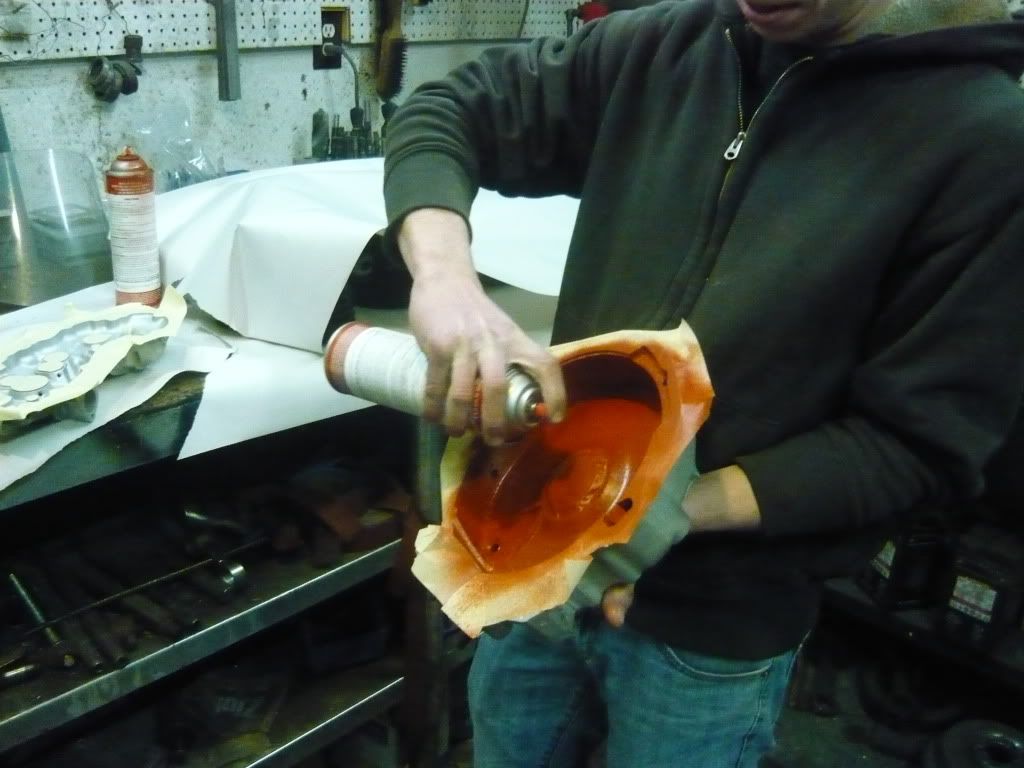
This is what I used, Matt and Carl use it on all their motors.
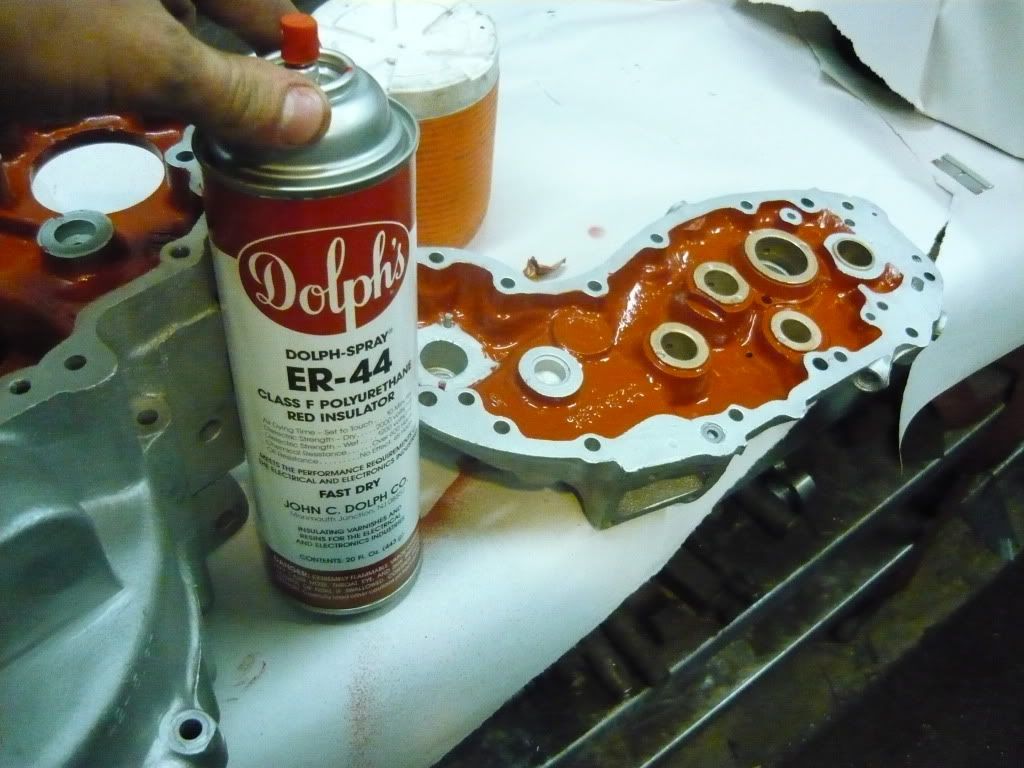
They are curing in the oven now and once they are cooled off I will start to put the motor back together! Not a bad way to end 2009 I'd say!
Comment