Tonight I got everything done on the frame except a little dressing of the welds. I found some defects when I was grinding them plus I filled in the tube that was worn away using a tig welder.
Then I proceeded to set the frame up on the table one last time and then I determined that it was slightly tweeked in the neck. I figured this out by laying 3" x 3/8" flat stock across the seat post tube to the front down tube. Then I made a pointer that fit in the neck and found that the pointer was off center between the flat irons that stuck forward from the frame.
I took six 1 1/2" split collars and put 2 on the seat post and I put one just above the front motor mount casting, one just under the neck and to on a big point I made for the neck. Where the frame was not 1 1/2" I had to make a split bushing to take up the slack. Now all of the collars were located on a tube that should have been centered over the center line of the frame. Then I cut some box tubing to use as a stand off to get the frame off the table surface. I located where I want the 4 pieces of box tubing to set and then used a transit to check that the table was perfectly horizontal. I ended up sticking 1/8" flat stock under one leg and that got the surface within .050" on all points. Then I set the box tubing at each of the 4 locations and repeated the process and then used shim stock under the box tubing to get within .010". I think welded down the box tubing to the table and laid the frame on it and welded the bottom side of the collars to the box tubing.
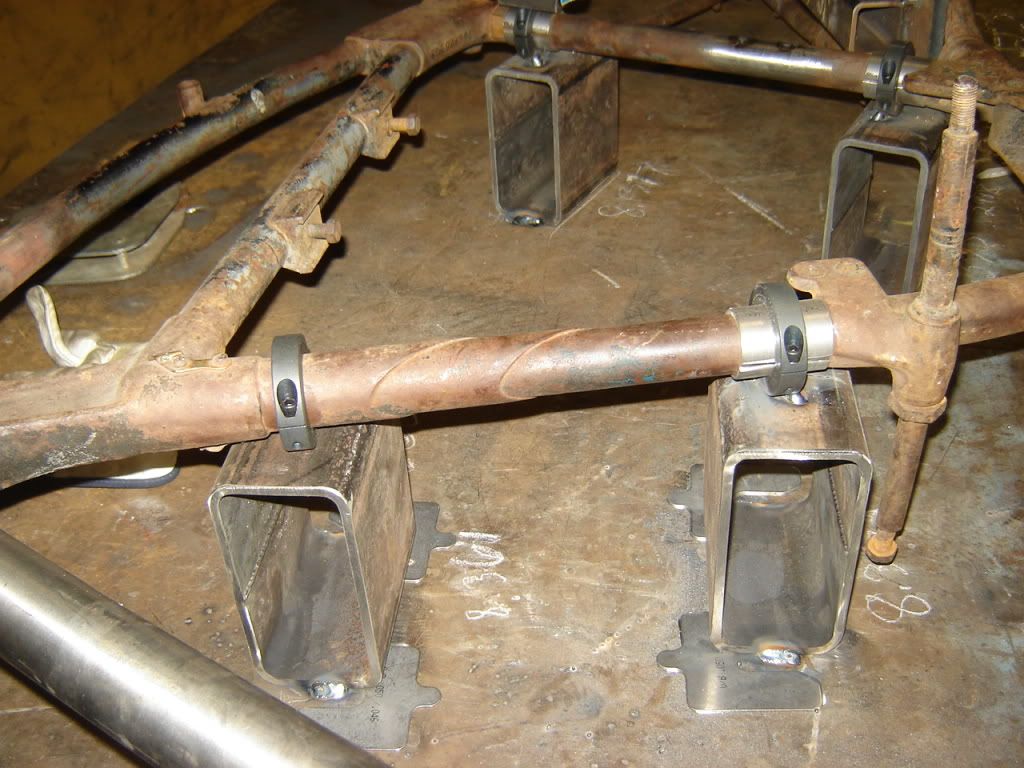
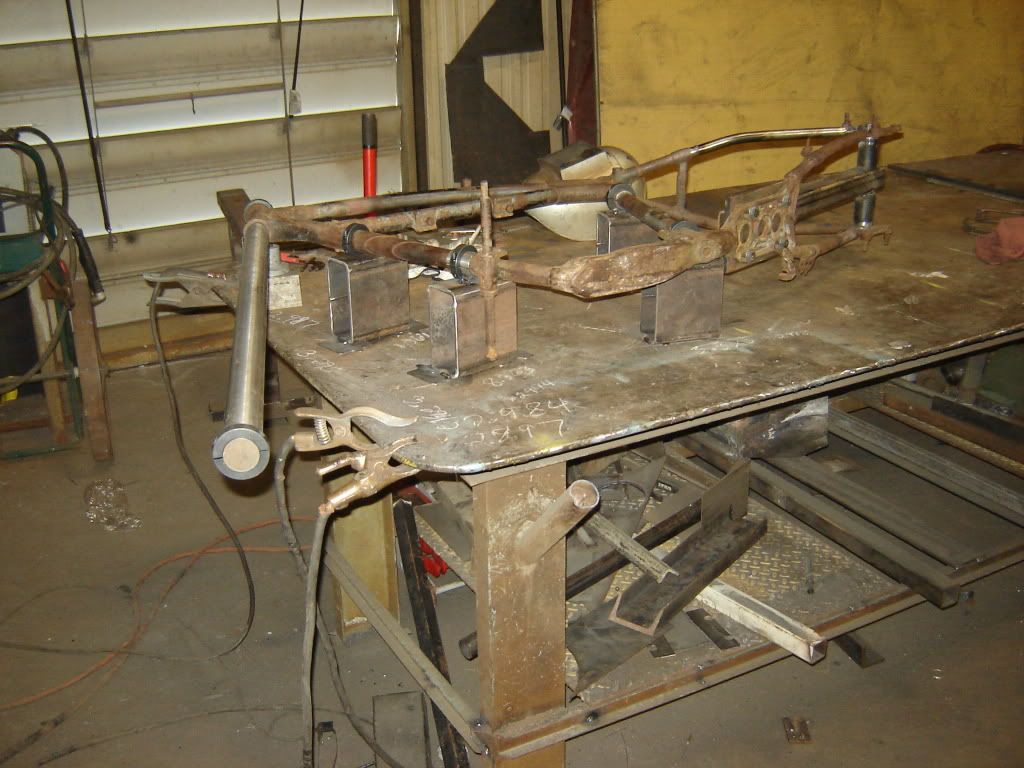
You can see the shims under the tubing to bring it all level.
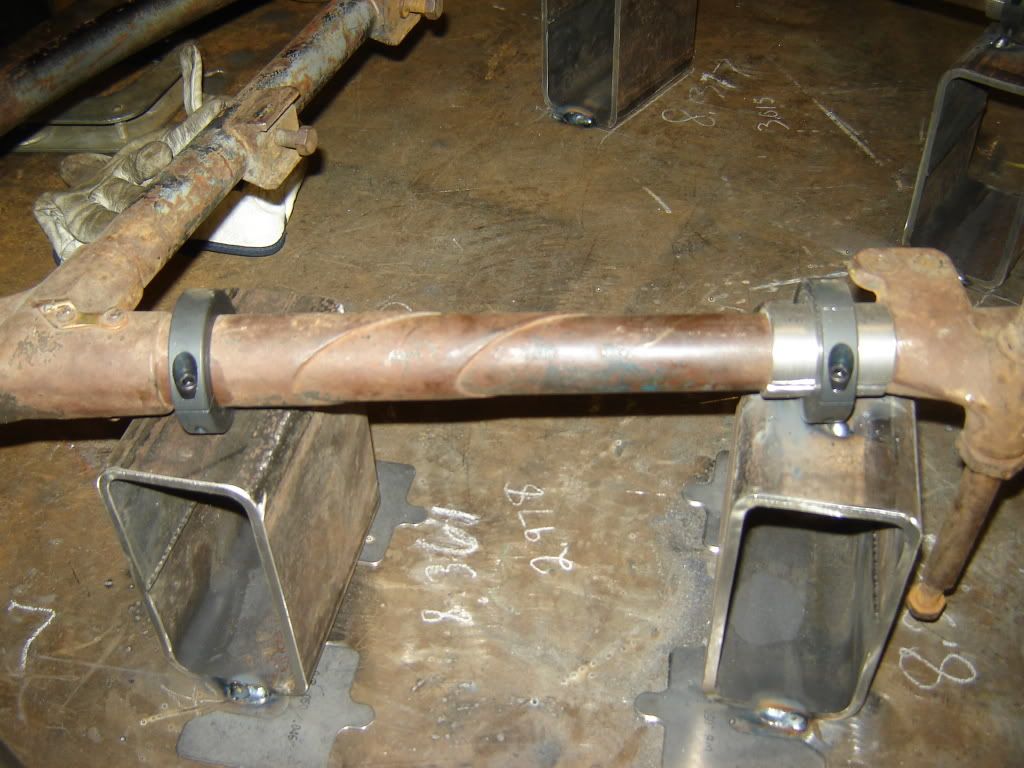
Now if the frame is straight all 6 of the collars top edge should be in the same plane or in other words have the same distance vertically when viewed thru the transit. We were able to confirm that the neck was off by a distance of about .220" from the collar just above the neck to the collar at the bottom end of the pointer. That is a distance of about 4'. Now what I had to due push down on the bottom end of the pointer and try to get the neck to stay where it was supposed to be. We found out that we were moving the whole neck down instead of twisting it like we wanted so I stuck a small machinists jack under it to hold it up on the upper end.
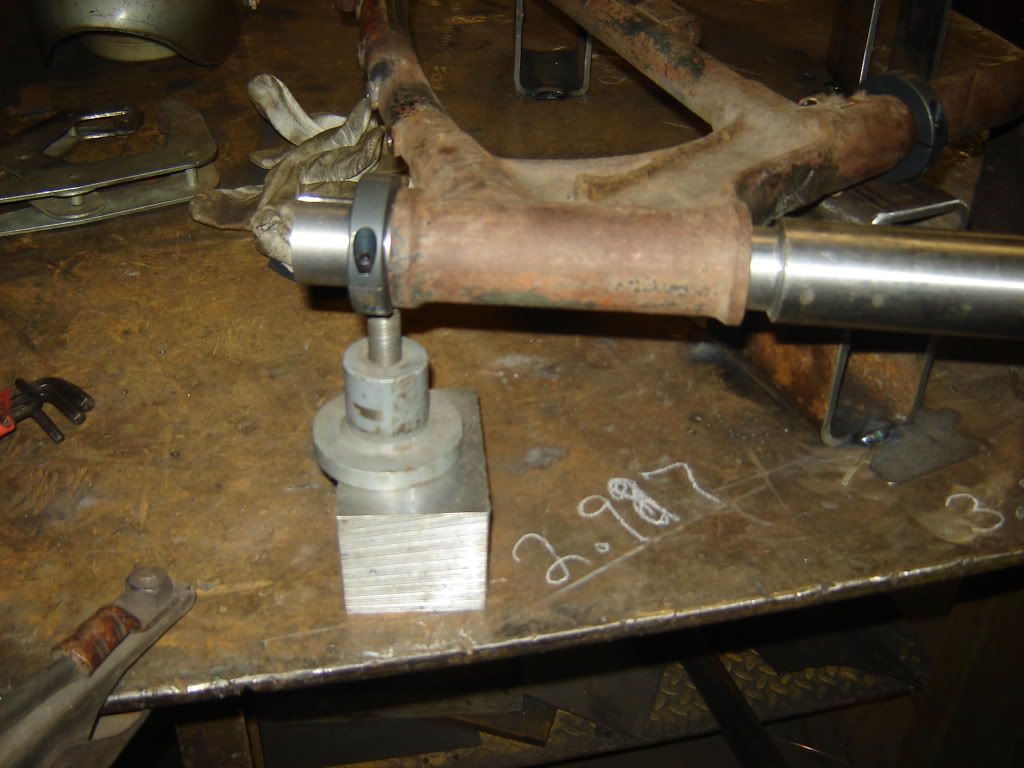
Then we repeated the process and it took a lot so we had to repeat and measure many times. Eventually we got it within about .010" and let it stand for a few hours and as expected the frame did go back a little to being bent so we had to repeat the process a couple more times until it stayed where we wanted it.
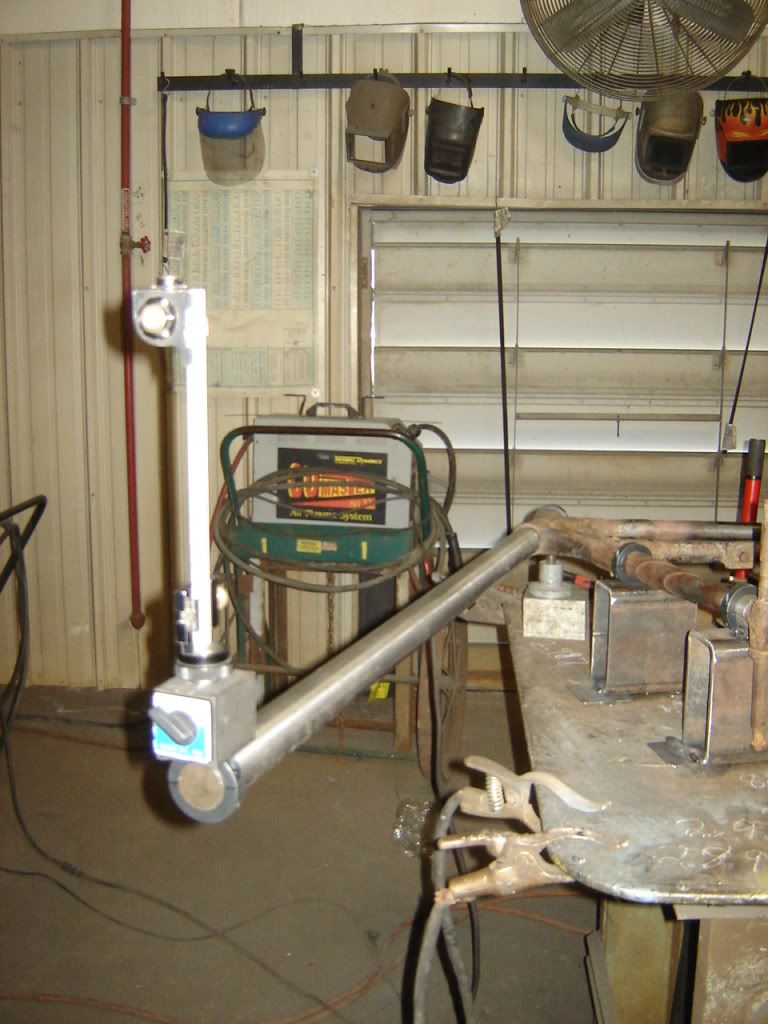
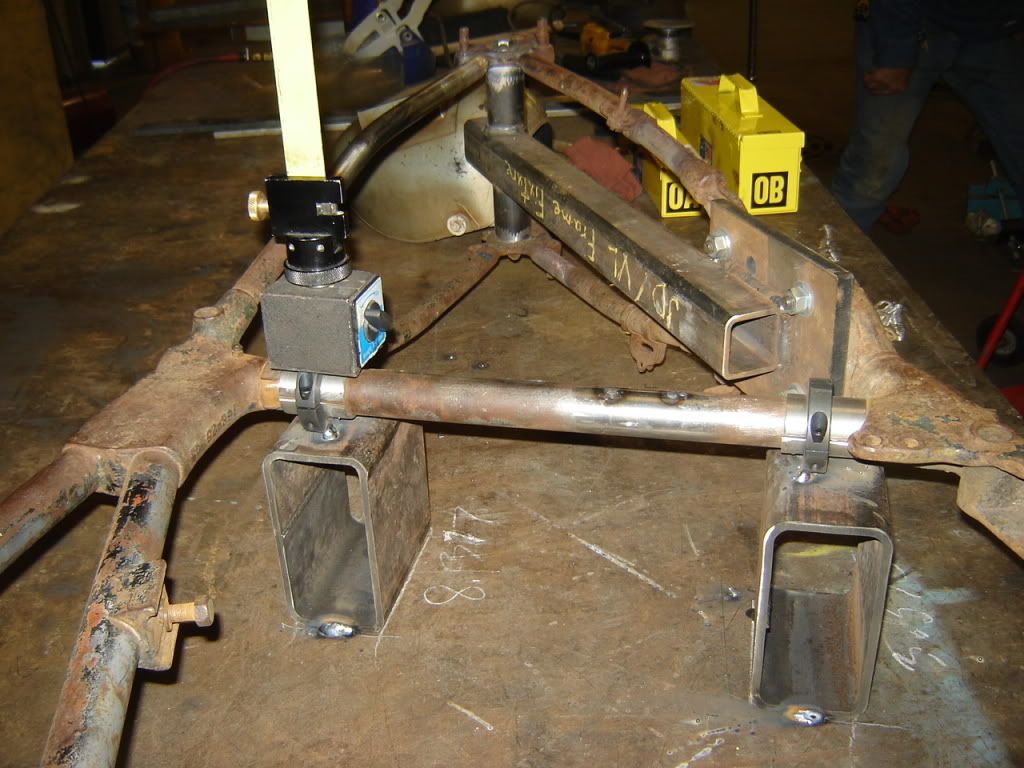
I hope you can understand what I did and hopefully the pictures can add something.
Jerry
Then I proceeded to set the frame up on the table one last time and then I determined that it was slightly tweeked in the neck. I figured this out by laying 3" x 3/8" flat stock across the seat post tube to the front down tube. Then I made a pointer that fit in the neck and found that the pointer was off center between the flat irons that stuck forward from the frame.
I took six 1 1/2" split collars and put 2 on the seat post and I put one just above the front motor mount casting, one just under the neck and to on a big point I made for the neck. Where the frame was not 1 1/2" I had to make a split bushing to take up the slack. Now all of the collars were located on a tube that should have been centered over the center line of the frame. Then I cut some box tubing to use as a stand off to get the frame off the table surface. I located where I want the 4 pieces of box tubing to set and then used a transit to check that the table was perfectly horizontal. I ended up sticking 1/8" flat stock under one leg and that got the surface within .050" on all points. Then I set the box tubing at each of the 4 locations and repeated the process and then used shim stock under the box tubing to get within .010". I think welded down the box tubing to the table and laid the frame on it and welded the bottom side of the collars to the box tubing.
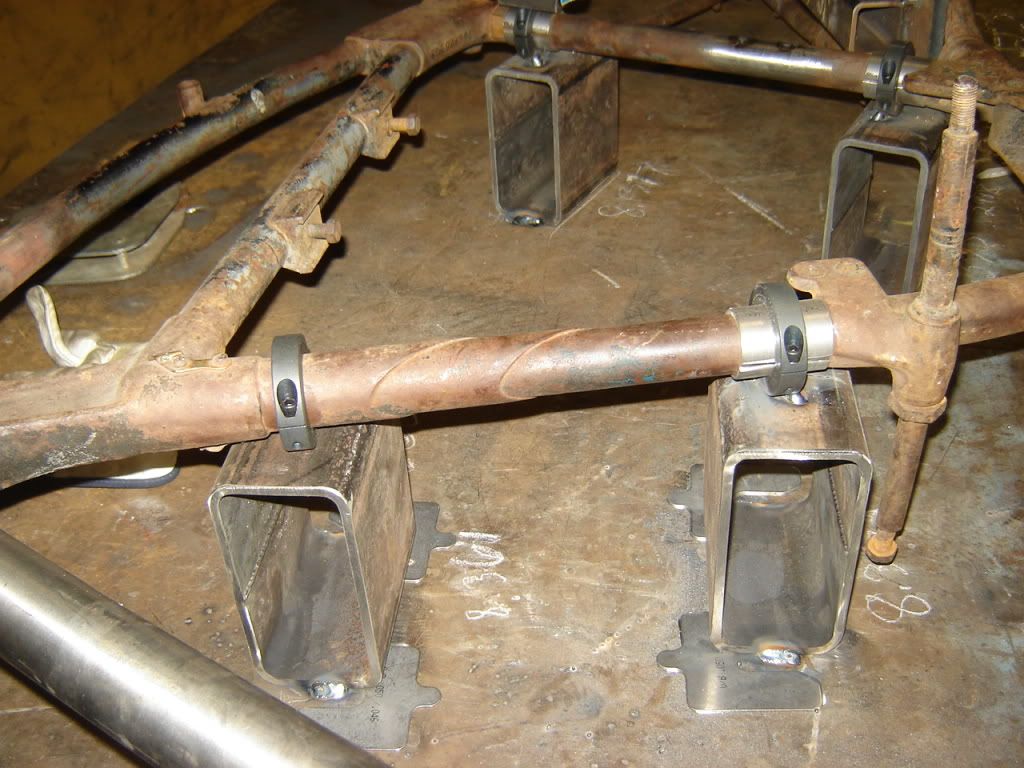
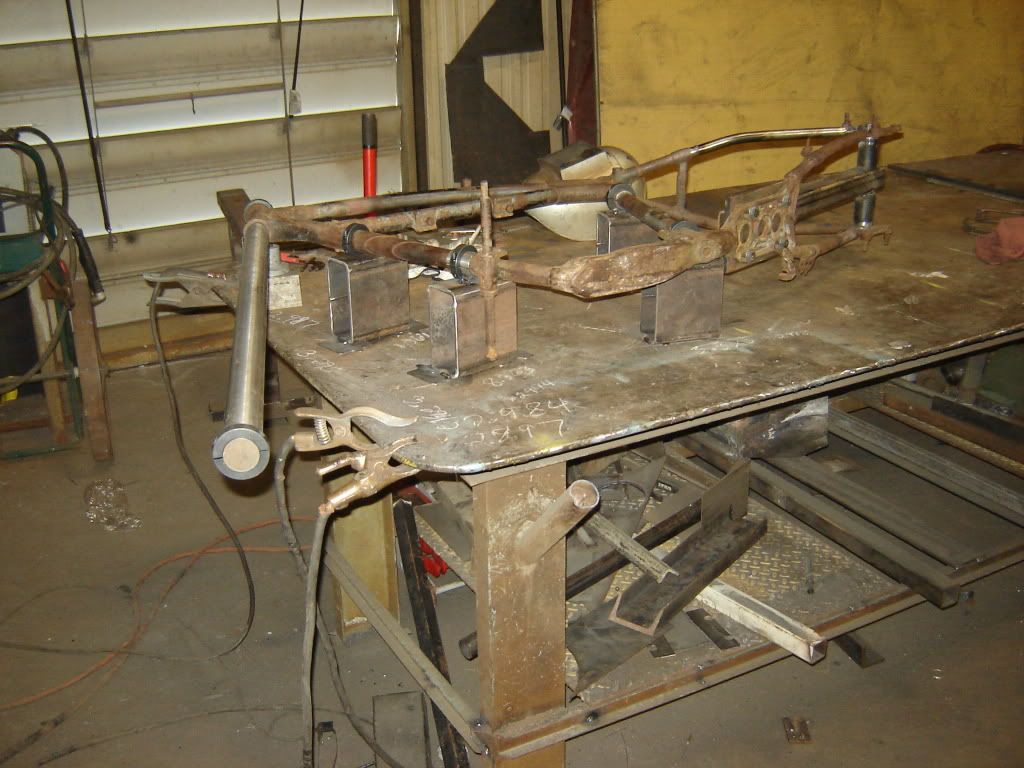
You can see the shims under the tubing to bring it all level.
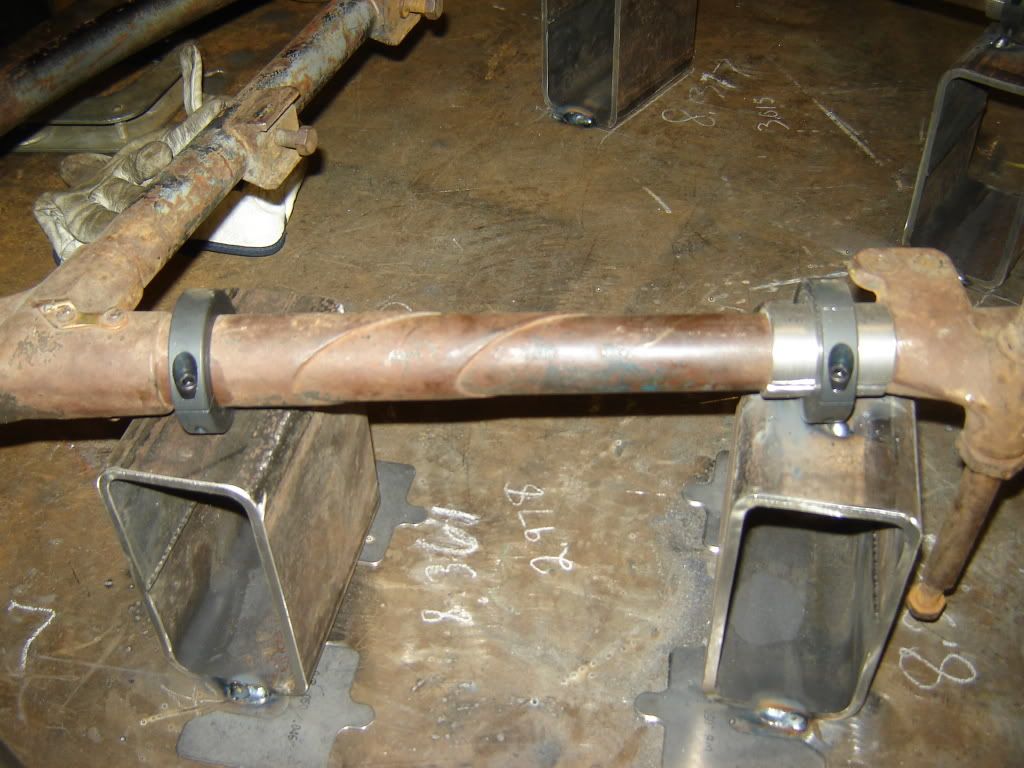
Now if the frame is straight all 6 of the collars top edge should be in the same plane or in other words have the same distance vertically when viewed thru the transit. We were able to confirm that the neck was off by a distance of about .220" from the collar just above the neck to the collar at the bottom end of the pointer. That is a distance of about 4'. Now what I had to due push down on the bottom end of the pointer and try to get the neck to stay where it was supposed to be. We found out that we were moving the whole neck down instead of twisting it like we wanted so I stuck a small machinists jack under it to hold it up on the upper end.
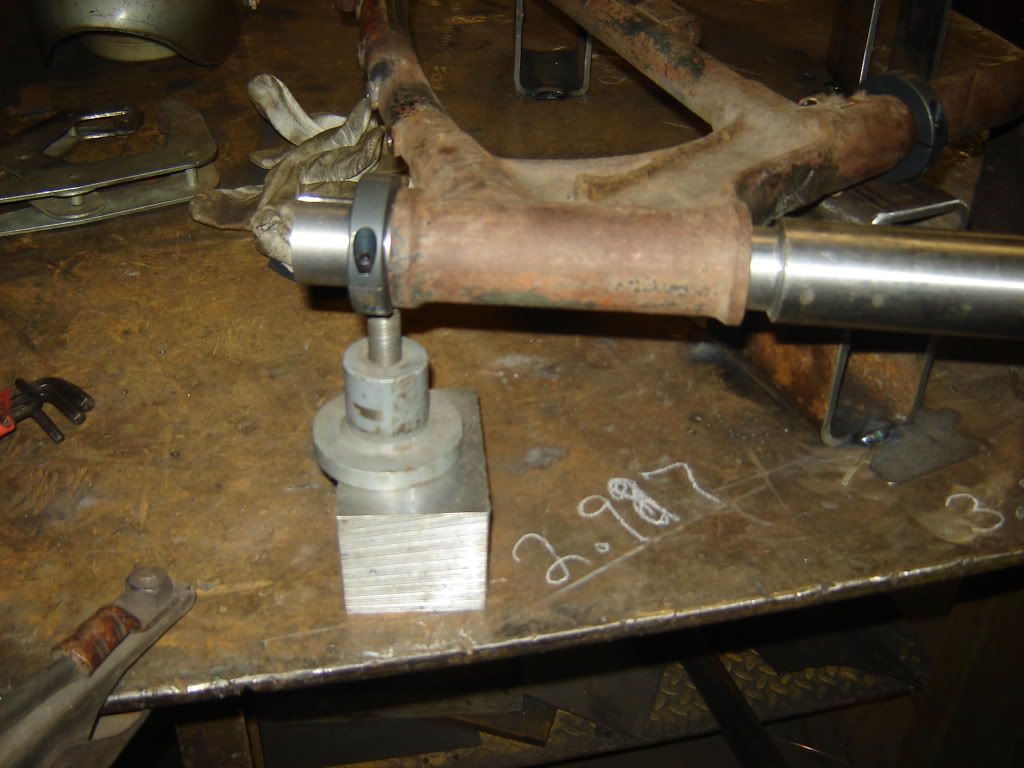
Then we repeated the process and it took a lot so we had to repeat and measure many times. Eventually we got it within about .010" and let it stand for a few hours and as expected the frame did go back a little to being bent so we had to repeat the process a couple more times until it stayed where we wanted it.
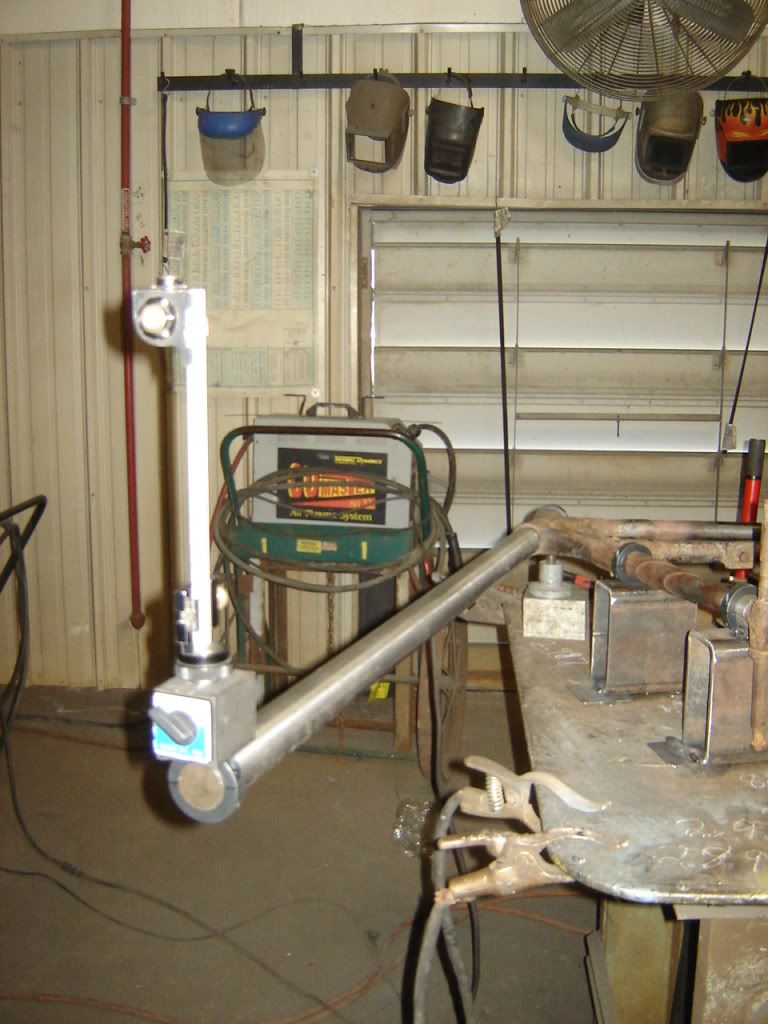
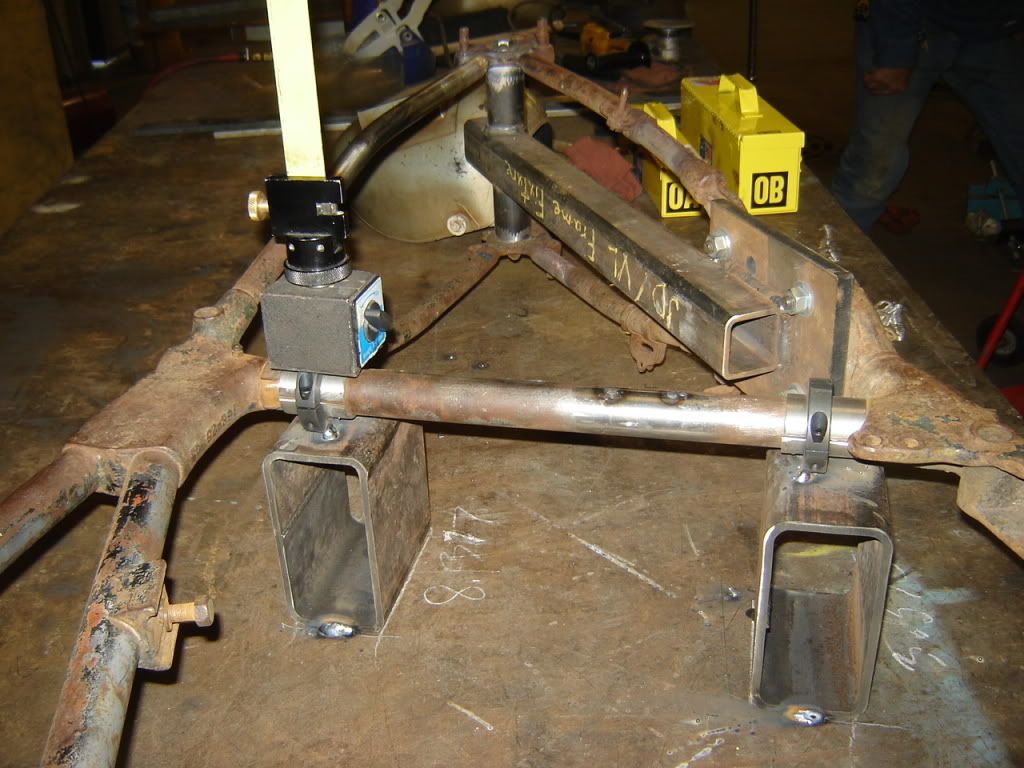
I hope you can understand what I did and hopefully the pictures can add something.
Jerry
Comment