My 1933 Harley-Davidson VL build is finally underway and I'll be cataloging the entire process with step by step articles on Riding Vintage. By the end of this project I hope to have a complete digital archive that someone could use as a blueprint to build their own V-series motorcycle. With that being said, any additional information, corrections, etc would be appreciated to make sure that everything is covered. This first article details how to prep and clean the engine cases before a complete engine rebuild.
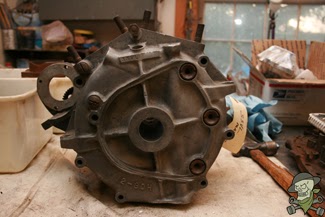
Building a 1933 Harley-Davidson VL: Preparing the Cases
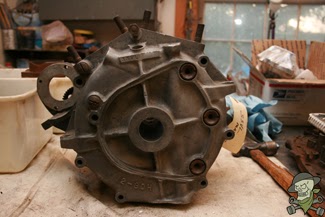
Building a 1933 Harley-Davidson VL: Preparing the Cases
Comment